Meloon Foundries llc
INFO
Partner Foundry
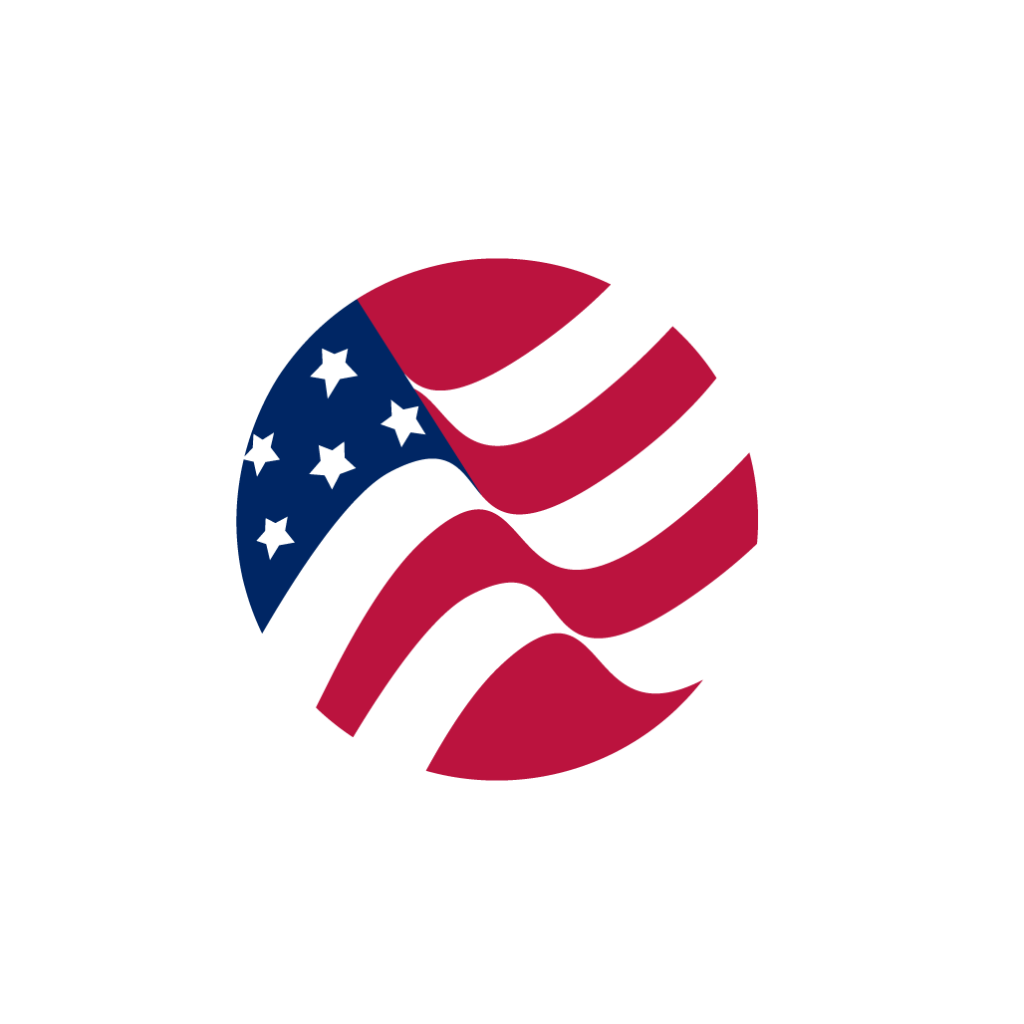
© 2025 Meloon Foundries LLC
Website & SEO By: MI Digital Solution
Meloon Foundries specializes in casting aluminum and copper-based alloys. Over 40 different alloys are cast for commercial applications serving more than 200 customers in the United States.
© 2025 Meloon Foundries LLC
Website & SEO By: MI Digital Solution