Meloon Foundries llc
INFO
Partner Foundry
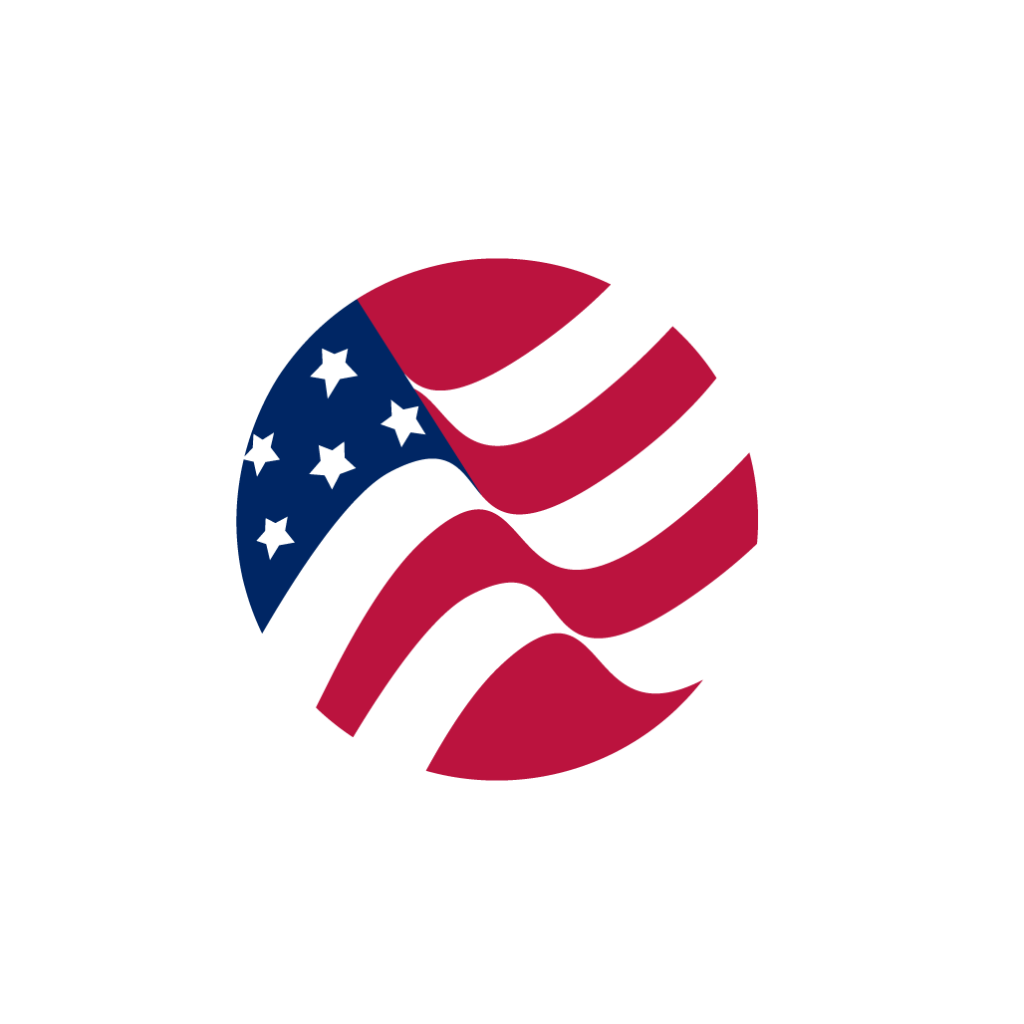
© 2025 Meloon Foundries LLC
Website & SEO By: MI Digital Solution
When designing a casting, active participation should take place between the Design Engineer, the casting producer and the machining source. Meloon Foundries LLC does this through direct contact with the casting buyer.
Aluminum Alloys | Copper Base Alloys | Casting Designs | Process Guidelines | Rapid Prototyping
Tolerances and Wall Section Considerations
The chart establishes general guidelines, the type of metal and other variables that will affect the casting cost directly linked to the process.
Our Processes | Other Processes | ||||
Green Sand Molding | No Bake Molding (Chemically Bonded Sand) | Permanent Mold Cast | Die Casting | Ceramic & Investment Casting | |
Tolerances, inches | +/- .030 in. | +/- .030 in. | +/- .050 in. | +/- .015 in. | +/- .020 in. |
Relative Cost in Quantity | Low | Medium High | Low | Lowest | Highest |
Relative Cost for Small Number | Lowest | Medium High | High | Highest | Medium |
Permissible Weight of Casting | Oz – 1500 lbs | 5 – 2000 lbs. | 100 lbs | 75 lbs. | Oz – 100 lbs. |
Thinnest Section Castable, Inches | 1/10 in. | 7/32 in. | 1/8 in. | 1/32 in. | 1/16 in. |
Relative Surface Finish | Fair to Good | Fair to Good | Good | Best | Very Good |
Relative Ease of Casting Complex Design | Fair to Good | Good | Fair | Good | Best |
Relative ease of Changing Design in Production | Best | Good | Poor | Poorest | Fair |
Range of Alloys that can be Cast | Unlimited | Unlimited | Aluminum-base and Copper-base preferable | Aluminum-base preferable | Unlimited |
Pattern or Tooling
A significant variable in the construction of a pattern is the determination of the shrink factor. The shrink factors vary for different metals and also the configuration of the part. The number of impressions, the gating system, the process or methodology will affect the casting cost. This is better left to the foundry and pattern maker to determine.
Aluminum Alloys
The chart provides typical mechanical properties for aluminum alloys and copper base alloys commonly cast by Meloon Foundries.
Alloy | Temper | Tensile Strength (ksi) | Elongation | Typical Brinell Hardness | |
Ultimate | Yield0.2% offset | ||||
319 | F | 27 | 18 | 2 | 70 |
SR319 | F | 31 | 27 | 1 | 70-80 |
355 | F | 23 | 12 | 3 | 65 |
355 | T-6 | 35 | 25 | 3 | 80 |
355 | T-51 | 28 | 23 | 1.5 | 65 |
356 | F | 24 | 18 | 6 | 40-70 |
356 | T-6 | 33 | 24 | 3.5 | 70 |
356 | T-51 | 25 | 20 | 2 | 60 |
443 | F | 19 | 8 | 8 | 40 |
535 | F | 35 | 18 | 9 | 60-90 |
713 | F | 32 | 22 | 3 | 60-90 |
ZA12 | F | 43 | 30 | 2 | 95-113 |
Copper Base Alloys
Alloy (UNS No.) | Tensile Strength (ksi) | Yield Strength with 0.5% Extension (ksi) | Elongation in 2 in. (%) | Hardness (BHN) |
C89833 | 37 | 17 | 30 | 50-65 |
C86300 | 119 | 83 | 18 | 225 |
C86500 | 71 | 28 | 30 | 130 |
C87200 | 55 | 25 | 30 | 85 |
C87500 | 67 | 30 | 21 | 120 |
C90300 | 45 | 21 | 30 | 60-75 |
C90500 | 45 | 22 | 25 | 75 |
C90700 | 44 | 22 | 20 | 80 |
C92200 | 40 | 20 | 30 | 60-72 |
C92700 | 42 | 21 | 20 | 77 |
C95400 | 85 | 35 | 18 | 140 |
C95800 | 95 | 38 | 25 | 150 |
C97600 | 40 | 24 | 20 | 75-90 |
Additional information may be obtained by contacting Meloon Foundries or The Non-Ferrous Founders Society.
Casting Design
A. Between two points in same part of mold not affected by parting plane or core
Specified Dimension, in. | Tolerances, in |
Up through 6 | +/- 0.030 |
Over 6 | 0.0300 +/- 0.003 in/in. over 6 in. |
B. Across parting plane. A-type dimension plus following:
Projected area of casting A1xA3 sq in. | Additional tolerance for parting plane, in. |
Up through 10 | +/- 0.020 |
Over 10 to 49 | +/- 0.035 |
Over 50 to 99 | +/- 0.045 |
Over 100 to 249 | +/- 0.060 |
Over 250 to 500 | +/- 0.090 |
C. Affected by core. A-type dimension plus following:
Projected area of casting affected by core,A3 x G sq in | Additional tolerance for core, in. |
Up through 10 | +/- 0.020 |
Over 10 to 49 | +/- 0.035 |
Over 50 to 99 | +/- 0.045 |
Over 100 to 499 | +/- 0.060 |
Over 500 to 1000 | +/- 0.090 |
Over 1,000 | consult foundry |
D. Dimension: Draft
Normally, a drawing does not show draft. Standard foundry practice is to “add” draft to the part. For the amount of draft required depends on design and type pattern.
E. Allowance for finish
Maximum dimension, in. | Nominal allowance, in. |
Up through 6 | 0.060 |
Over 6 to 12 | 0.090 |
Over 12 to 18 | 0.120 |
Over 18 to 24 | 0.150 |
Over 24 | consult foundry |
Process Guidelines
It is important that the foundry and the casting purchaser work closely together in order for the casting producer to make an acceptable cost effective part. Producing a casting for the first time entails a certain amount of trial and error.
It is an experienced-based development process. The expertise and past experience with similar casting configurations provide a guideline for the initial production. Usually the more intricate the casting design and the more drastic the change in section thickness the less predictable the casting soundness.
This is why it is important to consider location of isolated heavy sections, uniform wall thicknesses and correct placement or ribs and junction design. Visual casting soundness many times is not sufficient to verify acceptability and machining the sample casting prior to production release is important.
Specifications
Over specifying can increase the cost of a casting appreciable. Proper alloy selection, welding permissibility, correct choice of temper, and final inspection criteria all figure into casting cost.
Under specifying leads in many cases to misunderstanding between the casting producer and the casting supplier. Castings that are designed for critical applications require specific quality criteria. Selection of material that does not meet environmental or mechanical properties frequently leads to poor casting performance.
New Jobs
What are the requirements of first run or sample castings?
Rapid Prototyping
Rapid Prototyping is the developing of a temporary pattern or tooling from a 3-D computer design. This temporary tooling reduces casting time from months to days. The computer model is used as the blue-print and its dimensions to produce a model. Any rapid prototype pattern that is durable enough to withstand green sand or no bake molding can be used. There are several rapid prototyping processes and the selection depends on the application.
Meloon Foundries specializes in casting aluminum and copper-based alloys. Over 40 different alloys are cast for commercial applications serving more than 200 customers in the United States.
© 2025 Meloon Foundries LLC
Website & SEO By: MI Digital Solution